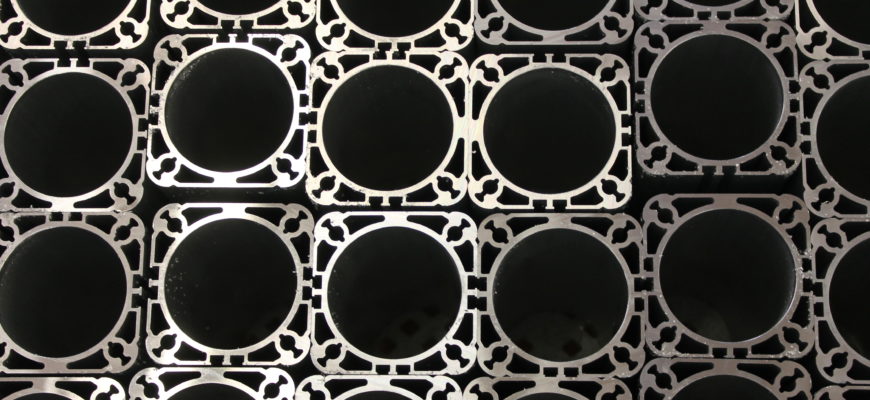
Pneumax was founded in the early seventies in Lurano, becoming over the years one of the major leaders in the production of pneumatic automation components. Today, the Lurano plant covers 94,000 m² divided into different units. Pneumax components are today distributed throughout the world in an increasing number of industrial sectors where systems for handling and manipulation with compressed air are required.
The pneumatic cylinders, in anodised aluminum and stainless steel, require a greater attention in the post-processing cleaning operation. This is because the cylinder stem must be protected, while the sleeve must be free of any stains and variations in the anodization colour.
To achieve the objectives set by Pneumax, Dollmar has designed a washing tunnel with 4 cycles of spray washing and final drying. The 14-meter long tunnel is equipped with a continuous conveyor belt in corrugated stainless steel. The pieces to be washed, of different sizes, are placed in baskets or directly on the conveyor belt.
The chosen washing process allows not to affect the anodization and to have no stains on the finished product.The entire production of about 5 million cylinders per year is washed in the tailor-made tunnel designed by Dollmar Meccanica.
A success for the customer and even more, a success for Dollmar who developed a solution that is reliable, functional and perfectly tailored to the needs of its customer.
Extract from ICT No. 3 February 2018 – full article